One consequence of the nation's economic downturn and the accompanying slump in general aviation was that some maintenance shops were forced to consolidate or close down, and many mechanics had to consider alternative careers. The result for airplane owners was the increased difficulty in obtaining high-quality maintenance services at a reasonable cost. For example, a friend of mine was unable to use his single-engine retractable for more than four months because of an ongoing landing gear extension problem. After one expensive repair, the problem recurred. In the interim, the maintenance shop had changed hands, personnel and landing gear expertise issues needed to be sorted out, and the airplane sat on the ground untouched. In another anecdote, the owner of a cabin-class twin was surprised to discover that the instrument shop he had used for years no longer was in business, and the technician in whom he had absolute confidence had moved to a distant airport. The result: increased costs in time and money for work he could trust.
Some owners may be tempted to save money by doing more maintenance work themselves within the limits prescribed by the FAA regulations. Others may accept less attention to detail than they've demanded in the past and spend less time looking over the shoulders of mechanics and examining paperwork, just to get their airplanes back into service. However, two accident investigations recently completed by the NTSB demonstrate that attention to detail and procedures is vital when it comes to aircraft maintenance, regardless of who does the work.
Beech M35
On May 19, 2001, about 10:32 a.m., PDT, a Beech M35 hit ground obstructions during a forced landing at North Las Vegas Airport (VGT). The aircraft's engine had lost power. The private pilot/owner was the sole occupant and received fatal injuries. The airplane sustained substantial damage. Visual meteorological conditions prevailed, and no flight plan had been filed.
About 10 minutes after departure, the pilot radioed the local controller at the North Las Vegas Tower and reported that the engine had no oil pressure and that he was returning to the airport. The airplane was cleared to land, but crashed about a ½ mile west of the runway. FAA inspectors conducted an on-site examination of the wreckage, which revealed that the engine oil filter element was hanging free from the filter base by the safety wire and that fresh oil was covering the fuselage underside.
An owner-assisted annual inspection was recently completed. The pilot had changed the oil and filter after the annual inspection. The changed element was taken to the mechanic who had signed off the annual so that it could be cut open for inspection. No mention of the oil filter change was found in the logbook.
In 1998, a remotely located oil filter system had been installed on the airplane. The installation consisted of a gold anodized base, which was attached to the firewall. The filter elements are screwed onto a threaded shaft, which is permanently factory-installed to a depth of about five threads and torqued to the filter base. Investigators noted that the installation of a filter element would require a blind insertion of the element onto the threaded shaft by touch, since the installation location was in the aft engine compartment on the forward side of the firewall. Examination of the filter base revealed evidence of thread damage to the first complete thread. The first five or six threads of the shaft were damaged, with a cross-thread appearance to the first two or three threads. Other threads were damaged and had the appearance of attempted file repair. Both ends of the shaft exhibited internal damage to the bore of the shaft. The mechanic told investigators that, at one time, the pilot/owner commented that he thought the filter base could be modified to accept different filter elements.
The NTSB determined that the probable cause of this accident was the pilot/owner's failure to correctly install the oil filter, resulting in oil exhaustion and a loss of engine power. Also causal was his attempt to modify the design of the oil filter element adapter by breaking the bond between the base and the threaded shaft, resulting in a loss of torque during filter-element installation.
Beech V35B
On January 26, 2003, at 5:36 p.m., a Beech V35B was substantially damaged during a forced landing at Pea Patch Island, near Delaware City, Del., following a total loss of engine power during cruise flight. The certificated private pilot and passenger received fatal injuries. Night visual meteorological conditions prevailed at the time of the accident. The flight had departed Wings Field (LOM) in Philadelphia, destined for Columbia Metropolitan Airport (CAE) in Columbia, S.C. An IFR flight plan was filed for the personal flight conducted under Part 91.
Review of FAA air-traffic-control data revealed that the flight departed about 5:10. At 5:12, the pilot contacted Philadelphia Departure Control and advised that he had an IFR flight plan on file. The controller acknowledged the transmission and provided the pilot a clearance, which included a climb to an altitude of 4,000 feet MSL. At 5:17, the pilot reported that he had reached 4,000 feet.
At 5:30, the pilot declared an emergency, reporting a terrible vibration, possibly an engine or propeller problem. The controller suggested that the pilot divert to New Castle County Airport (ILG), Wilmington, Del., which was eight miles behind the airplane. The pilot agreed, and the controller provided a vector to the airport.
At 5:31, the pilot reported that the airplane lost engine power. The controller stated that ILG was at the pilot's 11:00 position and seven miles away. At 5:34, the pilot reported that he was at 1,000 feet and descending, and wouldn't reach ILG. The controller replied that the emergency crew would be notified to respond to the landing area. About one minute later, the controller reported that radar contact was lost. The airplane impacted a wooded area about six miles south of ILG.
The pilot held a private-pilot certificate, with ratings for single-engine land and instrument airplane. His most recent FAA third-class medical certificate was current. On his medical application, the pilot reported a total flight experience of 2,960 hours.
According to a mechanic who worked on the airplane, the most recent annual inspection was performed on March 1, 2002. The mechanic estimated that the airplane had flown approximately 200 hours from the time of the annual inspection, until the accident. During November 2002, the mechanic completed a top overhaul of the engine, which included the installation of six new cylinders.
The engine was examined at the manufacturer's facility. The magnetos had separated from their respective mounts in the vicinity of the number-one and number-two cylinders, but they remained attached to the ignition leads. The magnetos, fuel pump, vacuum pump, starter and spark plugs were removed from the engine. Approximately three to four quarts of oil were drained from the engine.
A silicone sealant was observed along mating surfaces where the cylinders were attached to the case. Additionally, the substance was on the through-bolts.
The number-two cylinder was found backed off from the case. The engine case showed evidence of rub marks from the number-two cylinder. The number-two piston ring had shattered. The number-two piston skirt exhibited impact marks consistent with the skirt striking the case. The number-two connecting rod revealed elongated holes consistent with an overstress failure, and the rod cap wasn't recovered. Additionally, the top of the case exhibited two holes in the vicinity of the magnetos.
The engine manufacturer had issued a service information letter (SIL) 99-2A related to current authorized sealants, lubricants and adhesives. The SIL didn't list the type of silicone sealant found by investigators as an approved sealant on the mating surfaces of the crankcase halves or cylinders to the crankcase. Additionally, a review of a service bulletin (SB) 96-7B, which related to torque values for fasteners on all of the manufacturer's engines, stated: "Warning[---]the use of sealants or lubricants other than those specified by [manufacturer] on mating threads and between mating surfaces can cause incorrect torque application and subsequent engine damage or failure."
In a written statement, the mechanic reported that he added the sealant to the cylinder bases during the engine assembly. He said that he had referred to SIL 99-2A, but "[the type of sealant used] isn't mentioned, either pro or con." During a telephone interview with investigators, the mechanic stated that he hadn't referred to SB 96-7B.
The National Transportation Safety Board determined that the probable cause of this accident was the mechanic's improper engine overhaul. Another factor that caused the accident was the nighttime condition.
Peter Katz is editor and publisher of NTSB Reporter, an independent monthly update on aircraft accident investigations and other news concerning the National Transportation Safety Board. To subscribe, write to: NTSB Reporter, Subscription Dept., P.O. Box 831, White Plains, NY 10602-0831.
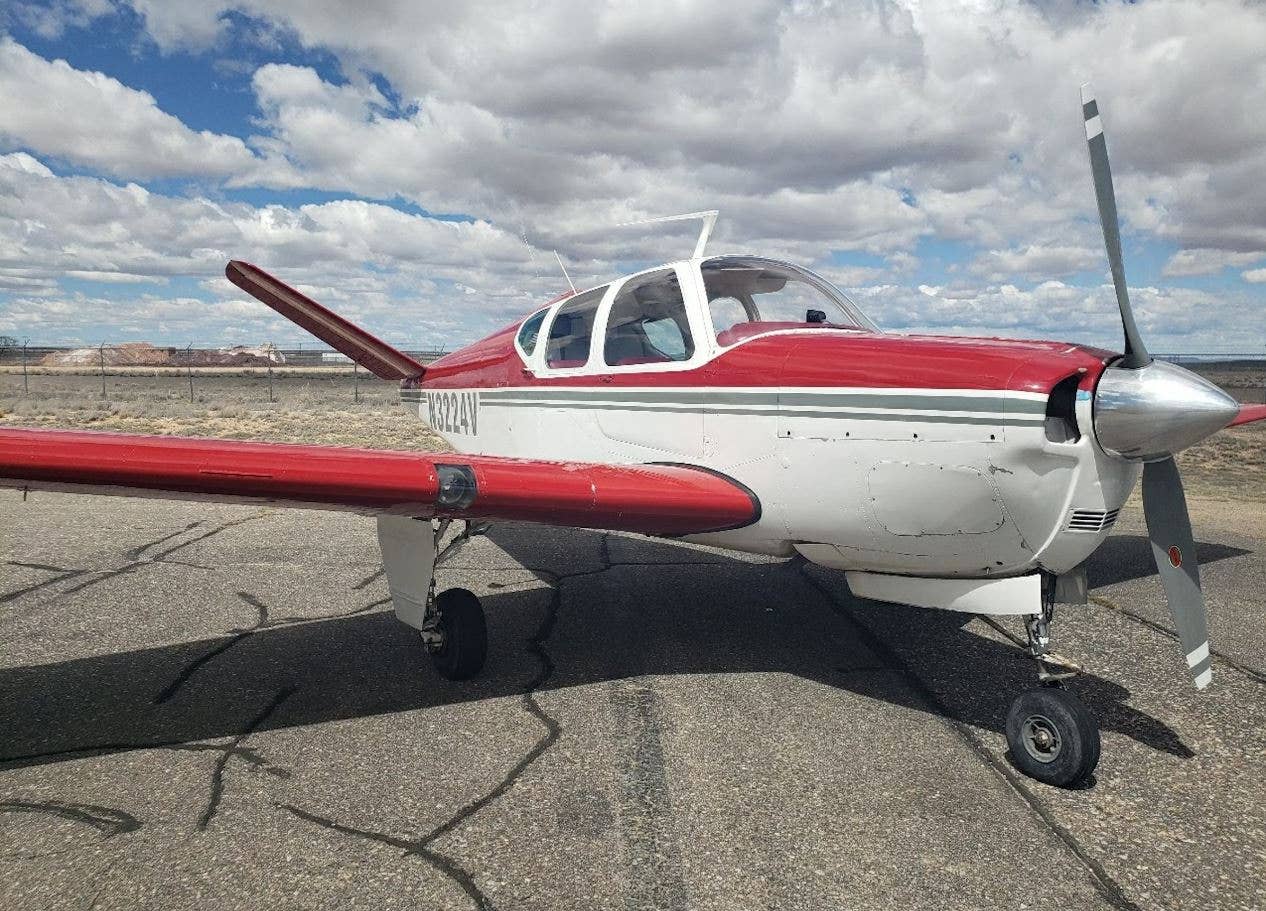
Subscribe to Our Newsletter
Get the latest Plane & Pilot Magazine stories delivered directly to your inbox