An Advanced Course In Engine Management
When you have to pay for fuel, repairs and overhauls, you’ll want to treat your powerplant to the values of science, not hearsay
![]() |
GAMI uses its two-cell engine test-stand to analyze its engines, employing unleaded autogas, a new spec unleaded Avgas and 100LL. The company also performed FAA certification testing for Superior's new XP-360 engine on one of its test stands. |
Today, bookstores have shelves of self-help and how-to books targeted at people just like me. You know, books like Brain Surgery For Dummies, Taxes For Dummies or The Idiot's Guide To Juggling. There is one guide, however, that you won't find in your local bookstore or, unfortunately, at your local airport. The Advanced Pilot Seminar (APS), better than books like Engine Management For Dummies, can only be found in Ada, Okla.
Walter Atkinson, George Braly and John Deakin developed the definitive course on Aviation Piston Engine Management. If you trust your life to a piston engine, it's a course that you should take. Braly provides the science and the hardware to the course, Deakin brings years of experience and Atkinson puts all the pieces together. Their Advanced Pilot Seminar is a direct outgrowth of the GAMIjector/lean-of-peak controversy. In short, the seminar, given every other month, takes engine management from a black art to a science.
For instance, would you like to know how to lean for density altitude, any density altitude, for any engine? The Advanced Pilot Seminar will tell you how.
In most hangar-talk sessions, these three men are the high priests of lean. But contrary to some pundits, they do not preach a faith based on leap-into-lean operations. They rely on science to answer the difficult questions; for them, theory must conform to facts and reality.
It all starts with what we know or what we think we know. Almost all airplane engines operate in a very harsh environment, sitting on a sun-baked ramp for days or weeks at a time. Languishing for months, they soak in the cold during bitter winters. After sitting mutely for long periods, they start in seconds, with temperatures rising from ambient to over 1,500 degrees. With minimum cooling, they produce 100% power for takeoff, followed by hours of high-power operation.
Our engines are expected to endure such harsh conditions, safeguard our lives and then abruptly start the whole cycle over again. We demand that our engines run smoothly, efficiently and reliably for 2,000 hours, regardless of whether it takes 10 or even 20 years to reach TBO. Aluminum and steel must perform at 100% in a moment's notice, with a thin film of oil as a lubricant, from zero to furious in minutes.
No other internal combustion engine is asked to do as much as the modern piston aviation engine. Perhaps racecar or marine engines come close, but the duty cycles and assumed failure risk don't even approach the environment faced by engines we fly behind every day. The basic design of the aviation piston engine hasn't changed drastically in decades. This is the 21st century, surely we can run our engines better now because we know more about them.
The answer is yes and no. In fact, the engineers who designed our engines and the big radials of the past knew what they were doing. Without modern technology and test equipment, they came pretty close to the answers that pilots ask every day.
The trouble is that we've forgotten those answers. How many hangar bull sessions discussed leaning techniques? How many times has your instructor talked about running rich of peak or lean of peak, and why? How does lead cushion valves, and extra fuel cool a cylinder head? All this corporate knowledge must be based on fact, right?
Those old-time engineers built and tested engines, producing power charts that we all use. They defined how exhaust gas temperature (EGT), cylinder head temperatures (CHTs) and horsepower relate to fuel consumption. During World War II, engineers plotted their test results from full rich to lean, and the Army classified the chart as top secret. Charles Lindbergh taught fighter pilots in the Pacific how to run lean of peak EGT, a technique that helped him across the Atlantic in 1927. Max Conrad used lean of peak to set distance records in his Comanche in the 1960s when he flew over 7,600 miles nonstop.
Lean of peak is not new and it hasn't been good advertising. When the marketing department is trying to make the latest Bonanza, Piper or Cessna look faster than its competition, they only want to know one thing. Where is the best power? The power charts very clearly show the best power.
Highest horsepower is achieved rich of peak EGT. A review of all Pilot Operating Handbooks from the 1950s to the 1980s shows a narrowing of engine management recommendations and displayed power charts. Speed was the important thing; maintenance and fuel consumption were not considered, easy assumptions to make when the cost of fuel was less than 30 cents a gallon and engine overhauls didn't represent 30% or more of the value of an aircraft.
There is a better way, and it has been used successfully for decades. The Wright 3350 radial occupied the pinnacle of piston-engine development and flew hundreds of thousands of hours on military airplanes and airline DC-7s. As a standard procedure, the engine was leaned to a 10% effective drop in the best power and lean of peak EGT. R-3350 operators were looking for lower cylinder head and exhaust gas temperatures, greater detonation margin and, coincidentally, lower fuel consumption.
Lean of peak may give greater range, but it meant flying slower and that was not a desirable option. Fast is what we wanted and fast was easy to find. Just lean to roughness and richen the mixture a bit. Voilá, 50 degrees rich of peak and very near the best power. Rough running was explained away in dozens of different ways.
When it's someone else's engine, advice like that is easy to follow. When you have to pay for the fuel, the repairs and the overhauls, it's a different story entirely. The trouble is how do we know what is right? How do we know the best way to operate our engines under any situation?
Advanced Pilot Seminar attempts to answer exactly these questions. You may be surprised, but the answers are not simple. Sometimes, you want to fly fast, sometimes you want to fly cheap. You can't do both. George Braly and Tim Roehl at General Aviation Modifications, Inc. (GAMI) were determined to find out why.
Carl Goulet, retired head of Continental Engine Engineering, suspected where the problem was. He challenged Braly to find out what was happening during a combustion inside the cylinder. The only way to determine internal cylinder pressures was to experiment, to directly read internal pressures created by every spark event. To answer that one question, GAMI went right out and built what may be the most sophisticated engine test stand in the world. At the seminar, you'll get to see this stand in action.
Horsepower production as a function of fuel flow and the resultant EGT and CHTs were well known. What happens inside the cylinder is not. Most aviation piston engines are timed to spark around 20 degrees before the piston reaches top dead center (BTDC). The internal cylinder pressure reaches a peak directly in proportion to the fuel-per-air ratio, and in Braly's test stand, those pressures are measured from the piston position of top dead center (TDC).
The piston engine is basically an air-cycle machine---hot expanding gas produces energy; in aviation engines, that energy allows the propeller to turn. At takeoff power when the throttle is wide open, the RPM and fuel flow are at a maximum. Any other setting changes the fuel-per-air ratio and the peak internal pressures. At rich mixtures, mass airflow governs horsepower, leaving extra fuel. At lean mixtures, fuel flow governs horsepower, leaving extra air.
The conventional wisdom is that extra fuel cools the process; the test stand shows conclusively that extra fuel delays peak internal cylinder pressures. Reduce the airflow and the fuel-per-air charge burns faster, reaching peak pressures earlier. When peak pressures occur closer to TDC, the actual value of peak pressure increases dramatically.
Bad things happen when cylinder pressures are high. Wear areas, like valves, are pressed harder into their seats and piston rings scrape harder against the cylinder wall. Fatigue is induced in high-stress areas of the piston, the rod, the crankshaft and the bearings. Higher pressures also mean thinner boundary layers between hot gases and the bare metal of the cylinders and pistons. Thinner boundary layers mean more direct heat transfer to the cylinder head, the valve and the valve seat. Higher pressures mean more wear and stress, and hotter temperatures, all of which decrease the engine life.
Lean mixtures also delay the peak cylinder pressures, delaying the maximum power pulse until well after TDC. The increased mechanical advantage of the connecting rod mitigates the power loss, but it's a fact of life that power drops off faster at leaner mixtures. As a matter of fact, you experience this effect every time you shut down your engine by leaning until fuel starvation.
What about rpm? How about lean misfire? How do I know what my ICP is? Should I install an engine monitor? Won't I burn my valves? What about deposits in the cylinder and on the piston? What is detonation and how can I avoid it? What does the temperature range of a spark plug mean to operation? Why do you say that I can run lean of peak if my engine shop or mechanic warn me about running too lean?
Lots of questions and lots of good reasons to attend the Advanced Pilot Seminar for pilots and mechanics. Attendance counts toward the FAA Wings program and the continuing education requirement for IAs. The bottom line is, if I told you all of their secrets, they'd kill me. But I'll give you a hint, one simple, important lesson from the test stand.
Real test-stand results show that similar internal cylinder pressures are reached at 120 degrees rich of peak and at 30 degrees lean of peak. Anything between these values is an area where internal cylinder pressures are too high and, in some engines, dangerously high. Essentially, this red box gets bigger at higher power settings, it's an operating area where fuel-per-air mixtures can do real damage to your engine.
So your mechanic is partly right, but for the wrong reasons. The real problem is not lean operations, but that we're not running rich enough. If you can't answer one basic question, based on fact, this course is for you. So, where do you run your engine?
If you want to know more or see the future through PRISM, call APS at (225) 925-2066 or reach them on the Web at www.advancedpilot.com.
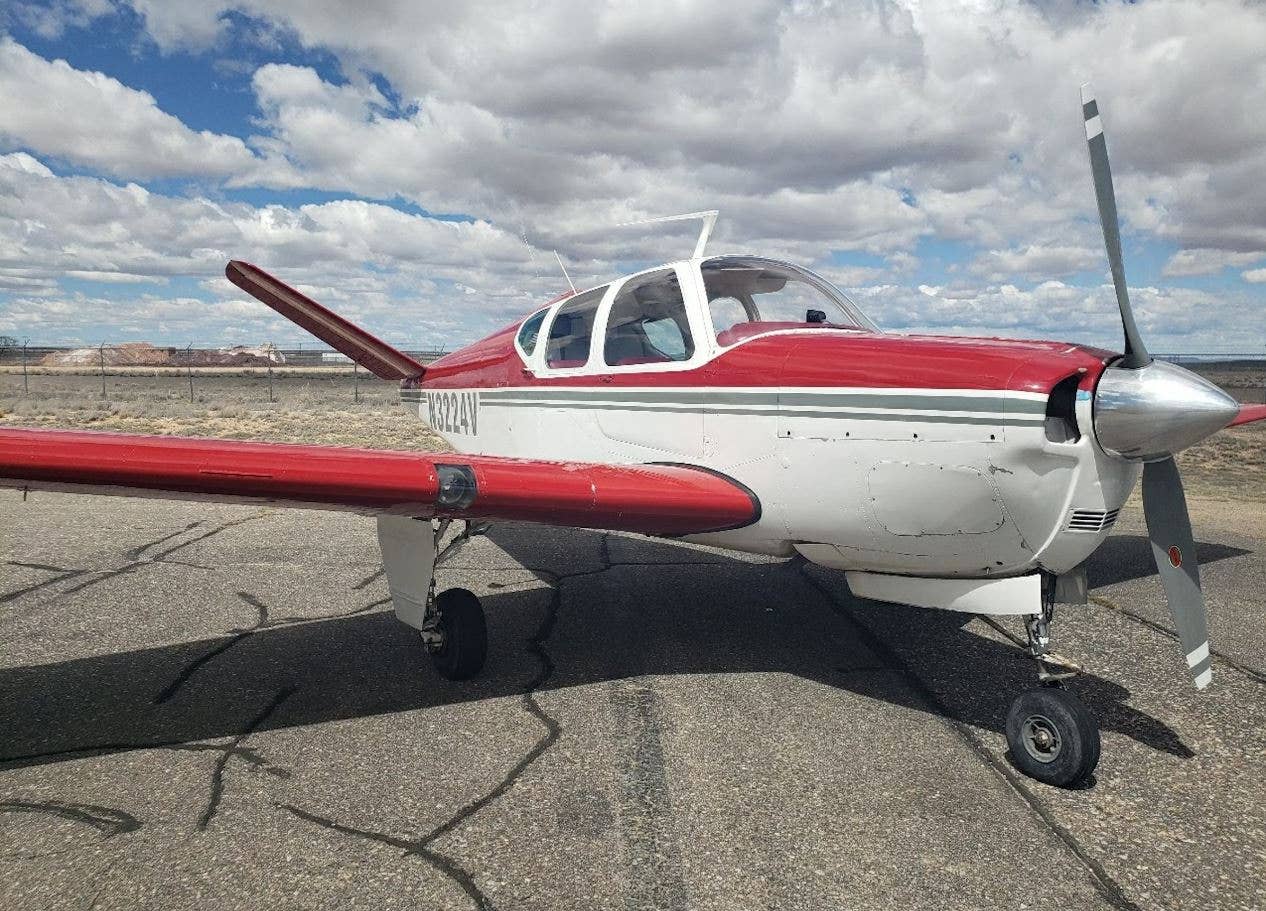
Subscribe to Our Newsletter
Get the latest Plane & Pilot Magazine stories delivered directly to your inbox