Why Deferred Maintenance Could Cost You Big Bucks
While it feels as though it’s saving money by putting off the repair or fixing it little by little, in the long run, in most cases it drives up the cost.
As an aviation community, we make a lot of noise about getting a good pre-buy inspection and thoroughly reviewing aircraft logbooks before making the leap into aircraft ownership. But can we say the same about encouraging our fellow owner/pilots to be meticulous in maintaining their planes?
We do an even worse job of educating new owners on the subject of deferred maintenance. Renting a safe, well-maintained airplane from your local FBO does not adequately prepare you for ownership, as I found out during that first year or two of aircraft ownership.
I learned only through trial and error---I made the errors, and it was a trial on my patience, not to mention my bank account. Some of the mistakes I made were on the conservative side of the coin, having the shop fix optional items out of ignorance and concern for safety, when, in reality, they weren't really safety issues at all.
Older airframes need expensive maintenance. It is reality. I have owned three aircraft from the 1970s (one as a partnership) and operated out of an airport near the ocean. My 1970s-era airplanes had their share of corrosion problems, and on more than one occasion taking care of it wasn't cheap.
I've been reviewing the amount of money I spent on my Cessna 182, which I sold recently, trying to understand why my shop's bills were what they were. I'll admit to being particular about how I maintain my airplanes, and over the four years I owned the Skylane, I don't recall ever having an annual where I did not do at least a few "optional" items.
While everyone has their perspective on maintenance, I got to thinking of the times I have chosen to defer maintenance and what I've learned from that decision.
As every airplane owner knows, these optional items are typically the ones the mechanic tells you would be great to make but wouldn't stop the plane from getting its signoff. One thing I discovered is that these "optional" items tend to move inexorably toward "required" if left alone long enough. In the example of my Cessna 182, corrosion issues caused me finally to act and replace the flap and aileron skins. The sheer volume of spot treatments in addressing the issue spot by spot was really adding up. So I bit the bullet and had the skins replaced. Likewise, cracked wheel leg fairings worsened to a point where it was prudent to swap them out, too, though I could have deferred.
There is no shortage of tough decisions to be made as an aircraft owner; deferred maintenance is one of those hard calls to make. While it feels as though it's saving money by putting off the repair or fixing it little by little, in the long run, in most cases it drives up the cost.
That's not universally true. There are smaller items, like Camloc fasteners, that do their job only because they're one of many fasteners in place. Likewise, cowl-flap rubber stops becoming ineffective at their job of sitting between the cowl flap and the bottom of the cowling. Not necessarily expensive but part of the list of items that can't be ignored forever.
Then there's the issue of repeated "fixes" that don't seem to stay fixed. When I look at my list from these past four years, one example that jumps out at me is moving to LED landing and taxi lights. Somewhere along the way, I got tired of replacing the old-school landing lights, which did not seem to tolerate the vibrations from the Continental O-470 mere inches behind them. The switch to LEDs cost a bit, but in the long run, it'll save me money.
Aircraft owners make these types of decisions throughout their ownership experience. As they do, they usually work in partnership with their A&P/IA. Those relationships vary in quality and commitment. Wittingly or unwittingly, a mechanic who's friendly toward deferring maintenance in the name of lower bills may be leading owners down a path that results in much bigger bills years down the road. From discussions with my A&P friends, this can be done in a misguided effort to keep the bill the same as last year, in order to keep the customer coming back, or it can be done to free up hangar space and get the plane back to its owner.
The owner/mechanic relationship is a partnership in every sense of the word; however, it is incumbent on the owner to be aware of the ramifications of their shared maintenance decisions. The owner who fully delegates this decision to their A&P runs the risk of unpleasant surprise down the road.
With older planes, ADs are a big part of the cost and maintenance picture. The truth is that not every A&P is diligent about researching AD compliance at annual time. Combine a complacent shop with an owner who isn't watching AD compliance either, and the next time the plane goes to a different shop, the resulting annual's price tag can be a shocker. And that isn't the fault of the new shop, either.
While one shop may choose to look past an issue, another may view its responsibility differently and be unwilling to sign off on an item previously labeled as "optional." For whatever reason, some IAs are more diligent than others and, again, in this litigious and FAA enforcement-heavy part of the world, it's hard to blame them.
One of the questions I ask my trusted mechanic when faced with an optional item is: "If this was your airplane, would you do it?" Over the years, I have gotten a "yes" a few times and several "I would probably hold off and keep an eye on it." This type of conversation is the very partnership that builds trust between the owner and the mechanic. Then again, the kind of response you get depends on the mechanic's attitude toward the business and the customer, and it can sometimes take an annual or two to get a good feeling for their perspective.
There's also the issue of building trust in the actual machine. Knowing you've maintained your plane well goes a long way toward helping us enjoy the flying part of aircraft ownership, rather than being distracted by worry of a failure at an inopportune time. For many owners, that alone is the worth the additional cost of an extra careful annual.
In my aviation career, I've been lucky to have never faced an in-flight emergency requiring interaction with the FAA. Speaking with pilots who have, I learned the FAA's initial line of questioning seems to center around aircraft maintenance. The FAA seems to be concerned with owners who skimp on maintenance or bypass it all together. Naturally, the inspector's line of questioning extends to the A&P/IA who signs off on the work, which explains the previously mentioned concern for liability.
Unlike some owners, who focus on a low bill, I want a mechanic who at annual time pays careful attention to detail and gives me an extensive list of what's going on with my plane, what I need to address, what I can hold off on and which items are a judgment call. From my personal experience, a good shop tries to keep these old planes going, balancing safety and cost.
My recommendation is to create a list of the "optional" items that come up during your annual inspection and prioritize them by running a review to determine the wisdom of deferring that fix or of writing that check. Here's a short list of questions to consider, and as always, many of these are best answered in discussions with your project manager at the shop.
- Will the money I spend on this item increase the value of my plane?
- Does this item run the risk of worsening with time? Is an early intervention the best medicine? (I can hear the "fix it when it breaks" crowd screaming already.)
- Should I get a second opinion from a more experienced aircraft owner or even from another A&P?
- How long am I planning on keeping this plane and will addressing this issue now help me sell the plane faster when the time comes?
- Does this work increase the safe operation of my plane and prevent a big surprise down the road?
Each of these questions is important in its own right. It's true that the last---will the procedure make it safer to fly the plane?---is clearly the most critical. At the same time, it's often the toughest one to answer conclusively.
Deferring maintenance isn't always the wrong call. Some fixes might not need to be made, while others might be completely inadvisable. At the same time, deferring any maintenance item without carefully considering the specifics of that potential repair is the kind of wishful thinking that we airplane owners can't really afford, at least not in the long run.
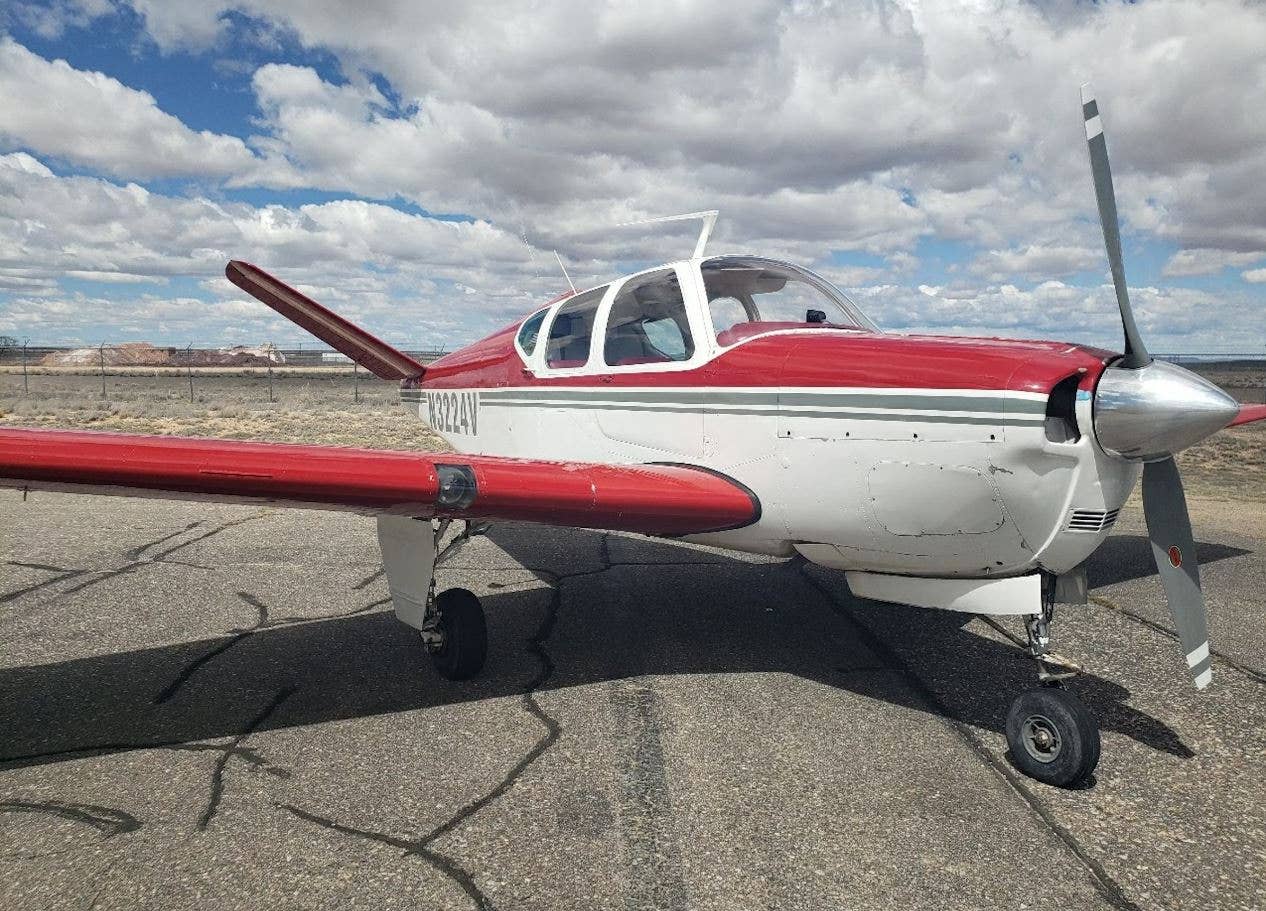
Subscribe to Our Newsletter
Get the latest Plane & Pilot Magazine stories delivered directly to your inbox