Building a Rudder at Zenith
When Zenith Aircraft CEO Sebastien Heintz invited me to attend the company’s annual homecoming event at its Missouri headquarters at the Mexico Memorial Airport (KMYJ) in September, he didn’t know…
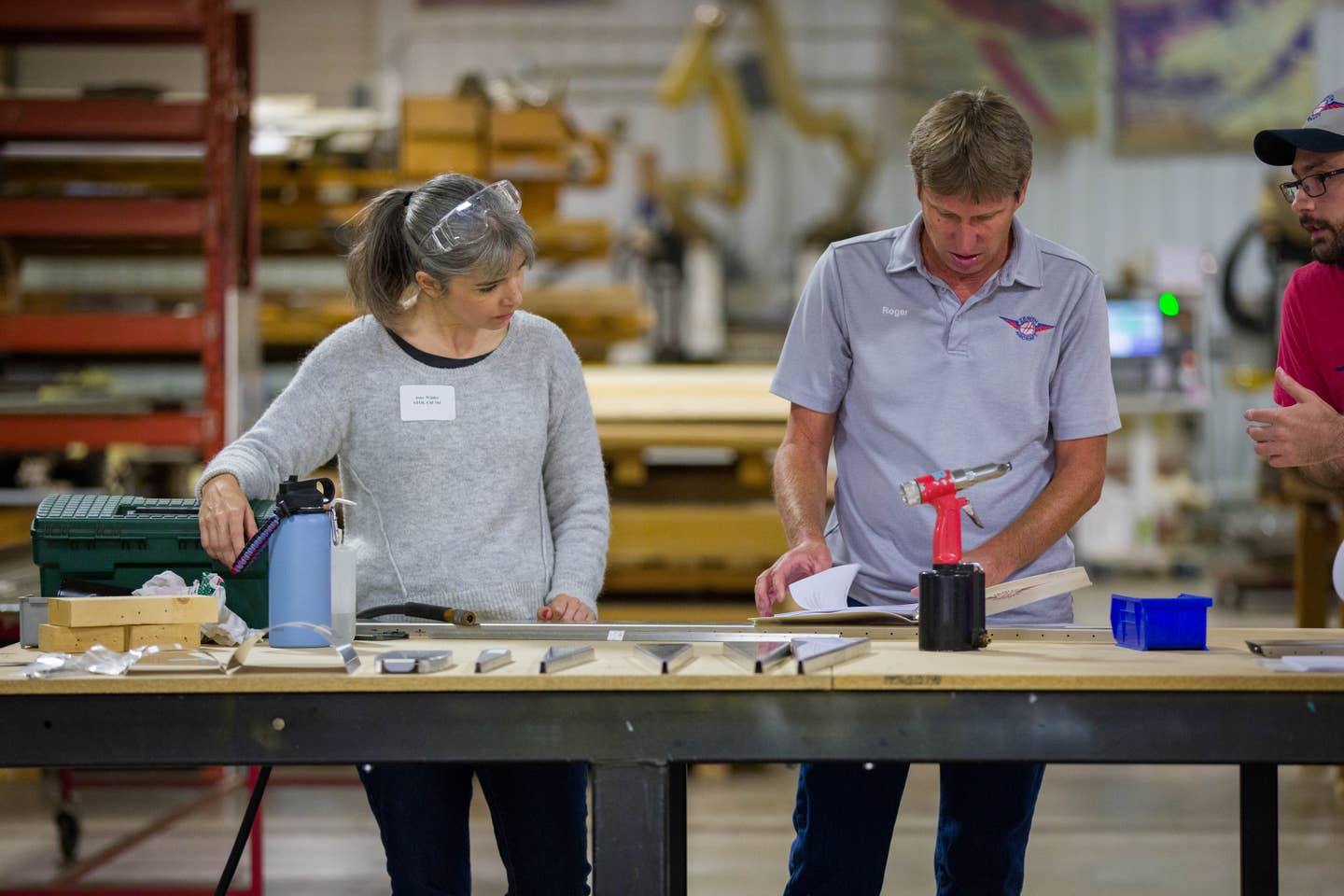
Zenith’s Roger Dubbert shows Wilder how to begin. [image: Paul Andrews Photography]
When Zenith Aircraft CEO Sebastien Heintz invited me to attend the company’s annual homecoming event at its Missouri headquarters at the Mexico Memorial Airport (KMYJ) in September, he didn’t know I’d been eyeing the company’s designs covetously for over two years—long before I found an editorial home at Plane & Pilot. I eagerly agreed to attend.
A death in my family rerouted my plans, but when Heintz extended a second invitation, this time to attend a rudder-building workshop the first week of October, I didn’t hesitate. I looked forward to visiting the premises (practically in my backyard, an hour’s drive from my house) to see the facility, meet more of the staff (I’d met only Heintz at EAA AirVenture last summer), and—what’s more American?—roll up my sleeves and rivet some airplane parts together.
I took it as a good omen that I was officially welcomed by Cleco the cat, who guards the premises from varmints and inspects newcomers. Apparently I passed muster. When I sat to complete paperwork for my CH-701 rudder project and sign in, Cleco made himself at home in my lap.
Heintz, son Calvin Heintz, and Roger Dubbert welcomed the workshop participants and introduced the tools and parts we would be working with for the next two days. Attendees came from across the U.S., mostly in pairs—either couples or friends attending together.
The Zenith trio showed us step one: removing labels carefully with acetone to prevent them from adding a millimeter of added depth to joins—something that could cause a headache later if not attended to first. They also demonstrated the use of cleco fasteners to hold parts in place for riveting and discussed riveting techniques.
And that was pretty much it—no dull lecturing or grandstanding. They let the participants jump in and begin, following step-by-step instructions in binders provided for the purpose. The trio remained available throughout the duration of the workshop, stepping in to answer questions, give advice at a key moment—Calvin was particularly helpful with timesaving riveting techniques at important points—and simply get to know the aviation enthusiasts who had traveled to take part in the event.
Participants also got to go on a short demo flight with Dubbert, and the entire group was treated to a tour of the facilities to see how outgoing shipments are organized from parts on the shelves and sheets of aluminum cut and punched on site to ease the building process for customers (who in the past needed to measure and punch holes for rivets as part of the build). Zenith is also growing, extending its building space in preparation for moving more of its operation south from Canada.
Not counting breaks for lunch, visits from Cleco the cat, tours, and demo flights—and simply taking time to get acquainted with other aviators—my CH 701 rudder took approximately eight hours of build time to bring together. Being on site for the project was extremely useful, as the Heintzes and Dubbert could step in to troubleshoot at key moments. According to Sebastien Heintz, the skills one earns in the rudder-building project will take a builder through most of the rest of the process, and the company is always glad to answer questions and help customers navigate through difficulties.
Takeaways
Through the process, I noted the following to pass along to those considering a build.
Buying or Building?
Dip Your Toe In
Building a rudder at Zenith is a great way to find out if this is the sort of project that you want to tackle on a larger scale. The workshop is dramatically inexpensive compared to buying the entire kit outright—or purchasing a new or used aircraft—and the camaraderie is great. Having access to the staff allows you to work through some of the common snags, thereby heading off time-consuming frustrations.
Pack Your Patience
Sebastien Heintz emphasized the importance of avoiding the urge to rush through the rudder project at the beginning of the workshop. This is absolutely one of those cases in which slow and steady wins the race. After several hours on the first day, I was fatigued and feeling pressure to continue. My rushing led to some fouled rivets, which Calvin Heintz expertly showed me how to remove.
Make It a Group Project
Bringing a partner, or involving one in your project overall, is a great idea. Having a second set of eyes, a second brain to puzzle things out when something doesn’t compute, and another pair of hands to pull stubborn aluminum parts into place when they don’t align just right is a huge timesaver. It’s also more fun.
It’s Easier Than You Think
One of my biggest takeaways from the workshop was that building an airplane from a kit could be easier and far more accessible than I had expected. There was a learning curve with the tools, and getting the pieces lined up can produce some frustration, but no special expertise, strength, or knowledge is required for the airframe build. If you have the time and are willing to invest that and some cash, it could be very rewarding. I realize my perspective is skewed by the relative quickness of the rudder build compared to the rest of the project.
In short, if you’re looking at options for your next, or first, airplane and are overwhelmed by options on the market, or by the thought of diving into a commitment, Zenith’s rudder-building workshops are a good place to start to determine if you’re ready. It’s a low-commitment, low-cost way to get started, and it’s enjoyable.
It might also be a great opportunity to get a middle school or high school kid in your life interested in aviation or interested in a STEM project. You can travel to Zenith, or you can look for workshops closer to home for you—the company regularly updates its upcoming events on its website and social media.
I came away with a new rudder—declared correctly constructed by Calvin—a sense of accomplishment and empowerment, and the enthusiasm to build an airplane. For now, the rudder remains in my living room until I decide whether to make the plunge. Zenith’s close proximity is alluring.
I could easily collect the horizontal stabilizer kit for my build and finish my empennage in a few days. I have room in my garage and a couple of teens who would love to build an airplane—and the educator in me thinks it would be a fantastic STEM and art project for them. I have a nearby airfield with an A&P who might be willing to help me work my way through avionics and engine installation. Temptations, temptations.
Editor's note: This story originally appeared in the Jan/Feb 2024 issue of Plane & Pilot magazine.
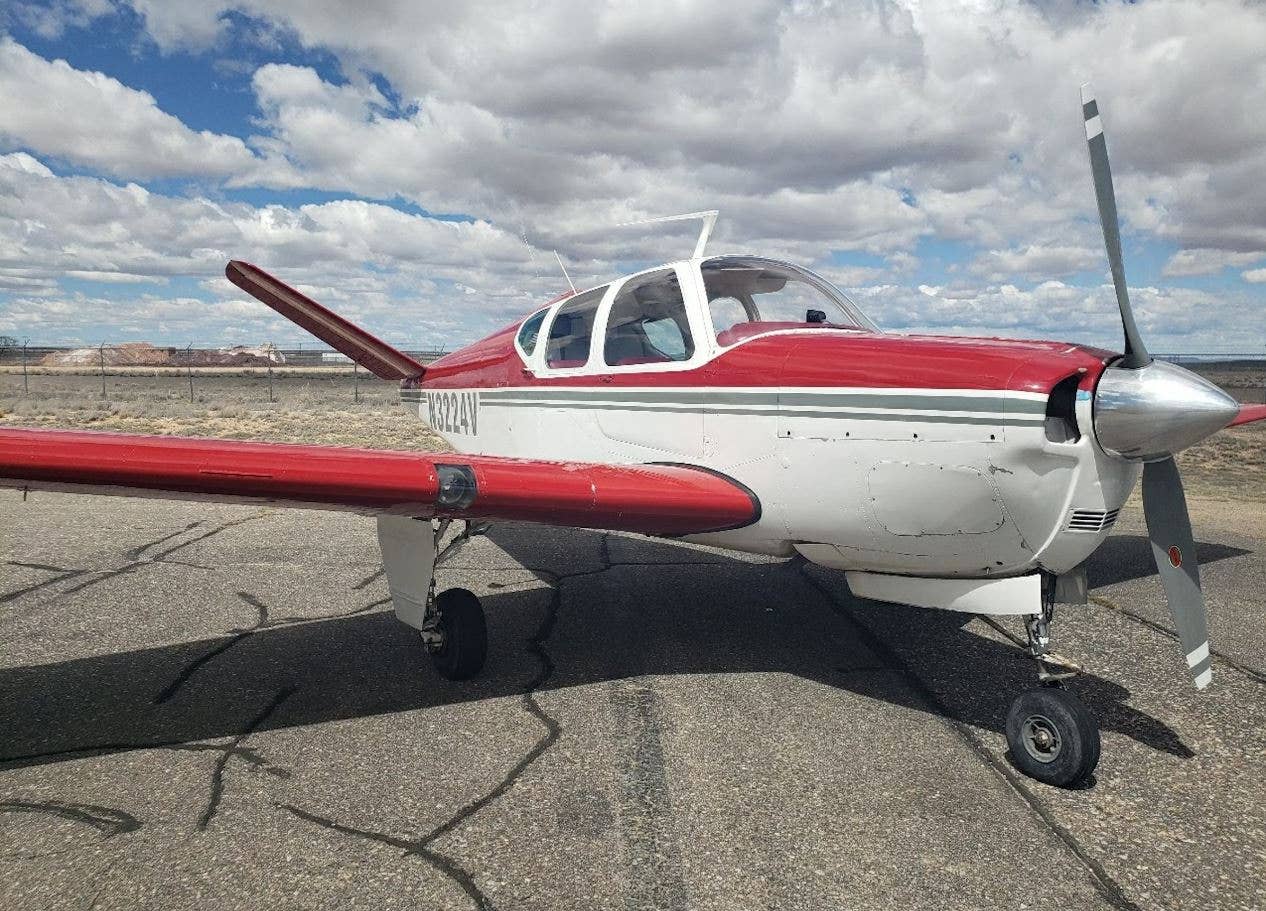
Subscribe to Our Newsletter
Get the latest Plane & Pilot Magazine stories delivered directly to your inbox